Page 1 of 1
Hello from NZ

Posted:
Wed Mar 06, 2019 10:43 pm
by madmax
Hi everyone,
I'm Jacob and I live in Rotorua.
I just recently purchased the plans for this bad boy. I am considering building in Carbon fibre.
I look forward to chatting with you all on the forums.
Jacob
Re: Hello from NZ

Posted:
Thu Mar 07, 2019 2:51 am
by Tim Ford
Hi Jacob, thanks for joining us!
Rotorua looks amazing! Can you sail in the lake there? Or do you have to head over to the Bay to sail?
Part of my boat was built in CF. I used doorskin okoume plywood and a couple layers of CF for my cockpit benches. Also I used it over foam for my rudder. I found it surprisingly easy to work with aside from sometimes being slightly difficult to determine if it was completely (or adequately) wetted out.
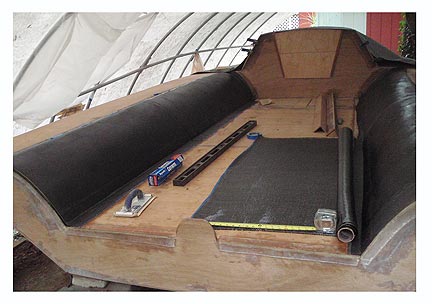
- i550July2011b.jpg (27.58 KiB) Viewed 6043 times
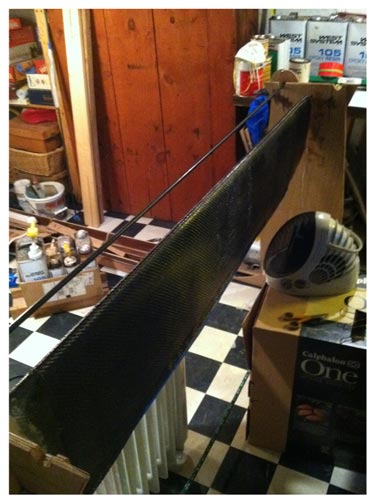
- i550ruddFeb2012a.jpg (36.31 KiB) Viewed 6043 times
Have fun and feel free to post pix if you want to, we'd love to see what you're up to!
Cheers,
--TF
Re: Hello from NZ

Posted:
Sat Mar 09, 2019 8:01 pm
by Warren Nethercote
Hi Jacob,
I presume you mean that you would like to use carbon fibre in lieu of glass fibre sheathing for the build, not build a CF boat per se. But a Brazilian started a divynicel cored glass panel boat (never finished?) that could as easily been a CF/foam/CF boat. The Gougeon Brothers build made a lot of use of carbon fibre in their i550, as is their wont
Gougeon Time-lapse build:
https://www.youtube.com/watch?v=GDs_BKdYjaQI used a fair amount for CF in my own build and regret not using more: it is MUCH nicer to work with than glass cloth and I suspect that the price premium isn't that bad. The Gougeon's use unidirectional CF across the boat whereas I used 9 oz three-layer biaxial cloth on my bottom, my cockpit side 'tanks' and around the stem. I also sliced up the biaxial and used it as biaxial tape for many joints. The panels that I sheathed in CF are much stiffer than those sheathed in multiple layers of glass, and smoothed out easier too and as such, were easier to fair.
Re: Hello from NZ

Posted:
Mon Mar 11, 2019 2:51 am
by madmax
Hi Tim,
the lake is stunning for small boats and there are quite a few larger yachts on the surrounding lakes including Lake Taupo.
The Bay can be used for sailing too and has a large fleet of various boats.
I'm lucky in that I have a friend who custom builds carbon fibre bikes for a living so I have lots of advice on tap.
I also have made my own vacuum pump so I can get good compression and wet out of the fibres.
Hi Warren,
I am intending to build a carbon sandwich boat with divinycell foam core.
Looking at 10mm foam which isn't much more expensive than a high quality 6mm marine plywood. ($110 vs $80 a sheet)
Going for 10mm should increased the stiffness of the boat given it will increase the distance between the carbon skins.
Thinner foam i.e. 5-6mm is hugely more expensive but I may use it for some applications.
Given there aren't any boats in my area I am aiming to build as light and stiff as I can.
I have a few other mad ideas I am considering for the boat but for the moment its all about analyzing the plans and coming up with a build plan for it.
I am half considering foils and a canting keel but then I have yet to come up with the actual designs to do this!
I am thinking of laminating up the three main hull panels and then bending them to shape using a female mold laminating the joins and inserting the bulkheads.
That way it will make a very stiff boat and ensure the shape is accurate.
Jacob
Re: Hello from NZ

Posted:
Mon Mar 11, 2019 3:10 pm
by Warren Nethercote
Jacob, the Brazilian build did exactly what you propose but with glass. They laminated frames and hull panels on the flat and then assembled them (or planned to do so - I never saw any assembly pictures) as for a plywood boat. I regret no longer having the web address for the that sandwich build.
I would offer a caution though. The forward part of the side shell is not really developable. A design with highly flared sides and a vertical stem never can be, although 6mm ply can be tortured enough to get away with it. If you did carbon/foam/carbon sandwich and increased the core thickness beyond that of the plywood boat you might find the CF sandwich skins too stiff to assemble. They might be too stiff even with a 6mm core.

If you just put the carbon on the inside of the shell panels before assembly and then added the outside carbon fibre afterwards you would likely get away with it.
The i550 class rules are not prescriptive on building materials so a CF/foam boat would not necessarily be illegal, although it might struggle a bit with 'lightness.'
Re: Hello from NZ

Posted:
Mon Mar 11, 2019 9:59 pm
by madmax
Thanks Warren,
Yes I had considered the stiffness of the panels before putting them into the mold, but many thanks for your thoughts.
I had considered just putting the pieces in as foam only and then molding the entire inside with carbon so that seams internally would be extremely strong.
Down side with this is that it means the outside will have more fairing work to do.
Conversely I had considered laminating the outer skin up in a female mold for a smoother finish.
I could then bond the foam into the outer skin or bond the foam and outer skin in one step.
The final step would be to bond on the inner skin, and finally the bulkheads.
Lightness I'm not too worried about as If other i550s are in the area for racing I can add corrector weights, if not I can leave them out.
Re: Hello from NZ

Posted:
Mon Mar 11, 2019 11:05 pm
by Warren Nethercote
You could build a female mould out of some pretty nasty stuff if you went that route.
Re: Hello from NZ

Posted:
Wed Mar 13, 2019 1:16 am
by Warren Nethercote
Re: Hello from NZ

Posted:
Wed Mar 13, 2019 12:57 pm
by Tim Ford
wonder what happened next?
Re: Hello from NZ

Posted:
Thu Mar 14, 2019 3:13 am
by madmax
interesting build such a pity we don't know how far they got with it.
Did some digging and I think at this stage 10mm foam for the hull sides and bottom, with 20mm for bulkheads etc.
The thicker the core the lighter the carbon skins can be and less resin needed so again weight savings there.
Added bonus is increased stiffness with thicker cores.
Re: Hello from NZ

Posted:
Sat Mar 16, 2019 2:46 am
by Mist
Hi,
Welcome to the club. I built my deck out of 1/2 A500 core cell foam. I used 6oz on the underside and 10oz on to topside. The deck is plenty stiff. The extra weight cloth on the topside is to minimize dents and dings when you kneel or drop things. Personally,if I were to build out of foam I use 1/2 A500 everywhere and 10 oz on all exterior surfaces. I wouldn’t bother with carbon because wet layup is quite inefficient on glue to resin ratio. A better choice is ‘S’ glass. It’s stronger then ‘E’ glass slightly more expensive and you can really dial in the amount of resin your adding during layup by sight. My 2 cents now that I built and sailed for a little while.
Re: Hello from NZ

Posted:
Sun Mar 17, 2019 8:18 pm
by madmax
Thanks for that Mist,
I am going to use divinycell 80kg/m3, looking at 10 or 20mm for the sides depending on how well the 20mm bends, and 20 or 30mm for bulkheads.
As a rough estimate the foam will weigh about 96kg all up and a further 70 kg or so for the carbon and the resin.
I have a vacuum pump so I can get good compaction of the carbon and minimize the resin content, my current ratios are about 60% fibre to 40% resin.
Warren, I am looking at building a female mold out of 4 or 6mm meranti or similar for the skins of the mold with stringers behind it over some OSB formers.
Jacob
Re: Hello from NZ

Posted:
Mon Mar 18, 2019 5:17 pm
by Warren Nethercote
Jacob, if you are building in a female mould then stiffness of the finished laminate should not be an issue, presuming you lay up the skins and foam wet-on wet or with resin infusion in the mould. Bending a 20mm thick cured, flat carbon/foam/carbon panel (or even 10mm?) into any curvature would be a diffrent story!

Re: Hello from NZ

Posted:
Mon Mar 18, 2019 8:33 pm
by madmax
Hi Warren,
yes I will do a wet on wet foam lay up and vacuum bag the foam down.
Bending a 20mm thick cured panel would be impossible, as would a 10mm panel from my test pieces that I did over the weekend.
A single skin of lightweight carbon cloth vacuum bagged down onto either side to the appropriate thickness of foam was impossible to bend in any meaningful way.
Re: Hello from NZ

Posted:
Sun Mar 31, 2019 1:50 pm
by ryderp
When I picked up my sails the sailmaker was building a GP26 on the ground floor of his loft. He built a female mold and formed the hull out of foam. However in order to get the panels to "comply" with mold, he built a homemade oven to heat up the panels first. He then vacuum bagged the outside layer of glass (or CF, I don't remember which - probably both). The inside surface was laminated after the boat was removed from the mold.
Re: Hello from NZ

Posted:
Sun Mar 31, 2019 9:40 pm
by madmax
Thanks for that ryderp.
I have done some trials with various foam thicknesses and 20mm is too thick to bend without modifying the foam by heating or scoring the panels, while 10mm is very flexible.
Doing some digging it seems like a lot of boats this size use 15mm foam which is I suspect probably about right for bending but a decent thickness.
Jacob
Re: Hello from NZ

Posted:
Thu Apr 16, 2020 1:52 am
by madmax
I have come up with what I think will produce a very very stiff boat and be light.
After some considerable experimenting with foam, epoxy, various grades of carbon fibre as well a different fabric types.
I am considering using 2x10mm skins bonded together for the hull sides, bottom, and deck. That way I can get the foam to bend easily to shape and still have the increased thickness of a 20mm foam. The outer skin will be 405g/m2 biaxial with a layer of 200g/m2 IM unidirectional under this for stiffness along the length of the boat. by doubling the foam thickness in the sides, their stiffness will increase 8 fold so well worth the effort I think. Inner skin of the hull will be a single layer of 405g/m2 biaxial carbon. Bulkheads I will do in 40mm foam with a single layer of biaxial cloth on each side.
Again building in a female mold.
Re: Hello from NZ

Posted:
Sat Apr 18, 2020 10:50 pm
by Warren Nethercote
Jacob, I hesitate, but in a boat this short (or of such low length to depth ratio) do you even need uni for longitudinal strength? My naval architecture is really, really rusty (bad joke - I was a big ship guy, not a yacht designer) but for something this small, short and stubby (not to mention no backstay), longitudinal bending loads are much less important than transverse and point loads. Of course, if I'm wrong it could be a sad and expensive experience.
With two layers of foam bonded together, through skin sheer strength, and so the strength of the hull shell, will be critically dependent on that adhesive layer, Applying heat to bend a thicker single layer of foam could reduce risk.
Re: Hello from NZ

Posted:
Mon Apr 20, 2020 12:49 am
by madmax
Thanks for that Warren,
Given its just a single layer of carbon otherwise except for extra at high load points ie mast and chain plates, keel box, rudder attachment. The extra layer is for the stiffness, but also my own peace of mind - as you say an expensive mistake otherwise. If it turns out to be overkill the next iteration of boats can be built without it

I have considered that about the foam layers, and it has been a concern for me too. Talking to my friend who builds bicycles and other things out of carbon getting the bond between the layers is critical and he did make several suggestions. One is to precoat the panels to ensure the bond between the panels is good as that way there aren't dry patches as the foam wont absorb the actual glue. Two I could also use vacuum bagging to help ensure a good bond. Heat is def a good alternative. I will do some digging on the heat required and how I would achieve this- heated box versus something like a heat gun.
Re: Hello from NZ

Posted:
Wed Apr 22, 2020 2:08 pm
by Warren Nethercote
I once had (but lost) a pdf technical package from Farrier and his foam-core building option may have required heating the foam to get it to conform to the hull shape (I do not remember ...). There must be Farrier builders in NZ who could advise on this.
Re: Hello from NZ

Posted:
Fri Apr 24, 2020 3:59 am
by madmax
Thanks for that I will have a look and I have also downloaded the Lloyds scantlings to look at for laminates and construction details.